We have a solution for you.
The combination of Just-In-Time manufacturing and the "transit time" imposed by the product pipeline from offshore manufacturing of OEM electronic components has forced suppliers to maintain substantial in-country product inventories to adapt to changes in OEM production rates and protect for any disruption in the transit pipeline. When the OEM requests a change to the module firmware or the end of a model year approaches, the cost of carrying this inventory rises dramatically. The ability to re-flash the module with the code change at the logistics center/warehouse with minimal labor costs can significantly reduce this overhead. EnGenius can help you meet these challenges with customized Pre-Delivery or multi-up Module Re-Flash stations.
You want proof? We have it.
Multi-Up Re-Flash
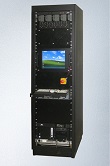
A change in module firmware has the potential to obsolete your product inventory in-country and in-transit. Re-flashing these modules allows you to adapt to these changes. However, re-flashing is a labor intensive process requiring unpacking/repacking, re-flashing, and record keeping. The EnGenius hardware and test software platform can provide an automated multi-up re-flash station that can significantly reduce this labor while improving quality by decreasing the opportunity for operator error.
Pre-Delivery Inspection
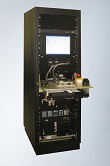
For some components, i.e., center stacks and infotainment systems, the difficulty and cost of replacing a faulty component and the negative impact on the customer experience is so large that the OEM requires a 100% inspection just prior to plant delivery. An automated test procedure that leverages network data to confirm switch activation and operator inputs can ensure that the test has been fully accomplished. If required, firmware re-flash can be included. Recorded data provides a quality audit trail.
Part Number Conversion
Model year change over can obsolete an unacceptably large inventory of components at in-country logistics or warehouse facilities. In many cases, the only difference between "old" and "new" components is a new version of the firmware and a label. In some components, such as center stacks or instrument panels, a switch position or indicator can be populated/de-populated as part of the conversion. Part number conversion allows you tailor the product mix to match OEM build schedule or carry your inventory into the new model year.
In-Plant Recertification
As any supplier of electronic modules or audio systems knows, the return of hardware that failed during vehicle manufacturing but return "No Problem Found" when retested can be a significant cost driver. Adding a recertification facility in the assembly plant or in a facility nearby can reduce the cost of returned components or provide early warning data on emerging problems. A recertification test system can be built as an enhanced EOL tester that runs the tests required to confirm correct operation or flash updated module firmware without the cost and time associated with a trip back to manufacturing.
Experience
EnGenius has been providing engineering and manufacturing test solutions for vehicle multiplexed network systems for over 30 years. Applications have included vehicle manufacturing end-of-line testing, dealer diagnostics systems, module programming, software validation, and module DV & PV test systems. Although our MultiCom family of vehicle network interface adapters has been used by OEMs and their suppliers since 1989, the hardware abstraction inherent in our test environment supports other network interface hardware such as J2534, Vector®, and National Instruments®. In addition, EnGenius supplies custom multiple station test systems for DV, PV, and other engineering test applications. The test applications can be developed in EnGeniusTEST, LabView®, TestStand®, C/C++, and/or Visual Basic.